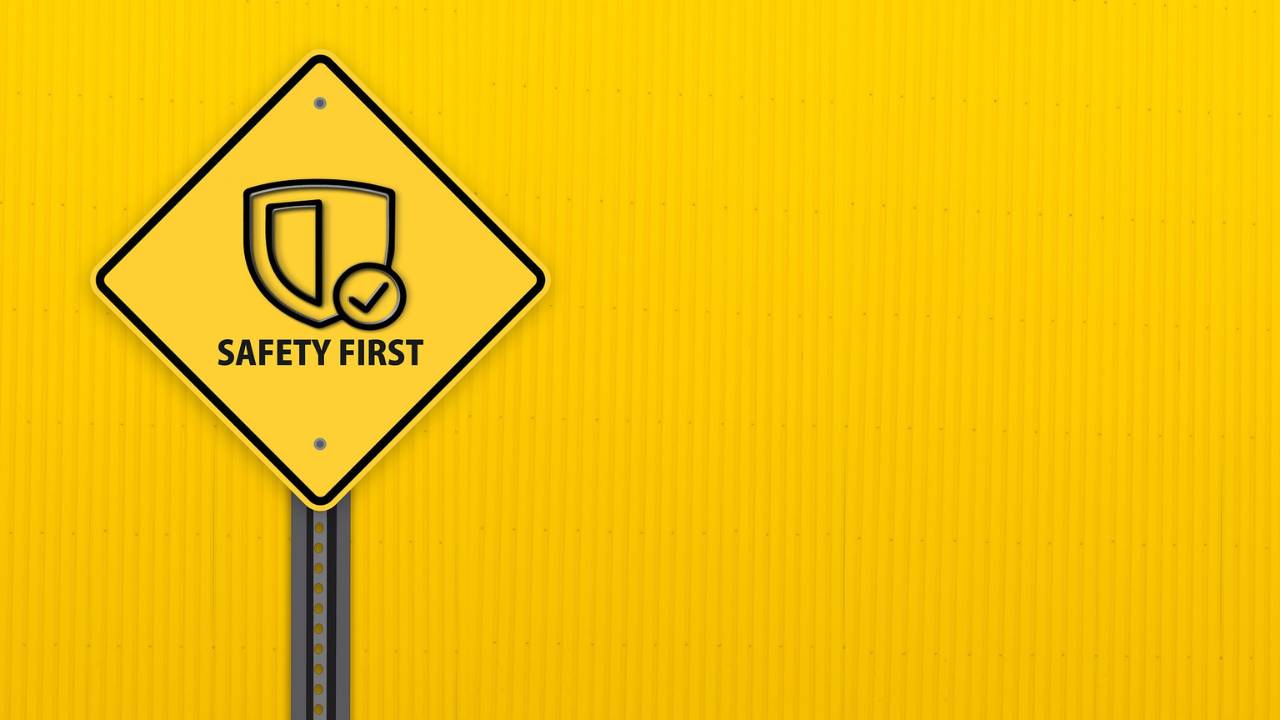
For small businesses across Ireland, unexpected repair costs can wreak havoc on carefully planned budgets. Among these, office repairs consistently rank as one of the most common – and frustratingly preventable – expenses. When equipment fails suddenly or facilities require emergency maintenance, businesses face not just the direct repair costs but also the hidden expenses of operational disruption, lost productivity, and potential safety incidents.
What many business owners fail to recognise is that a systematic approach to preventative safety checks can dramatically reduce these unexpected costs. By identifying and addressing minor issues before they escalate into major problems, organisations can maintain smoother operations while protecting their bottom line. A loose connection caught early might cost €20 to repair, whereas the same issue left unattended could result in equipment failure costing thousands – or worse, trigger an electrical fire causing catastrophic damage.
The Hidden Costs of Ignoring Office Safety
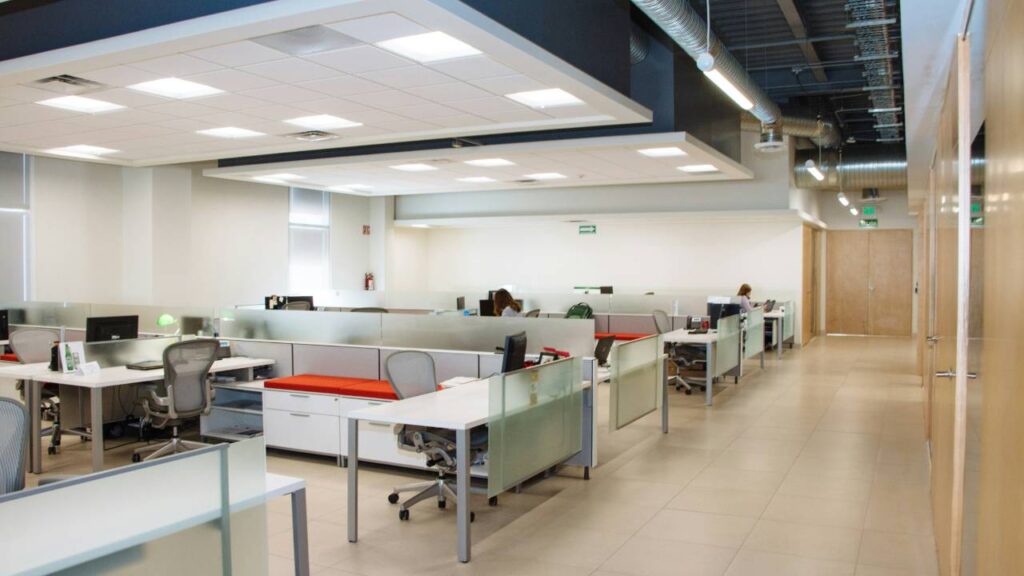
The true cost of neglecting office safety extends far beyond the immediate expense of replacing damaged equipment. These hidden costs accumulate gradually but can ultimately prove devastating, particularly for small businesses operating with limited financial reserves.
Delaying basic maintenance or ignoring minor faults can quickly result in your business losing money through equipment damage, downtime, or failed inspections. Consider a typical scenario: a slightly damaged power cable might initially cause intermittent connectivity issues for an essential piece of equipment. Left unaddressed, this minor problem could eventually cause a short circuit, damaging not just the original device but potentially affecting other connected equipment or even causing an electrical fire.
The financial impact cascades through multiple channels:
Direct Repair and Replacement Costs: When equipment fails catastrophically rather than being maintained preventatively, the repair costs typically increase exponentially. Complete replacement often becomes necessary, requiring capital expenditure that wasn’t planned for in the budget.
Operational Downtime: When critical systems fail unexpectedly, operations grind to a halt. Every hour of unplanned downtime translates to lost productivity, missed opportunities, and potential revenue loss. For client-facing businesses, this downtime can damage professional relationships and reputation.
Insurance Implications: Many insurance policies include clauses requiring reasonable care and maintenance. When claims involve equipment that clearly suffered from neglect, insurers may reduce payouts or deny claims entirely, leaving businesses to shoulder the full financial burden of incidents.
Regulatory Penalties: The HSA has the authority to issue improvement notices, prohibition notices, and financial penalties for workplace safety violations. These official actions not only carry direct costs but can trigger additional expenses through mandatory remediation requirements.
Employee Productivity and Morale: Working in environments with obvious safety issues negatively impacts employee morale and productivity. The constant worry about potential hazards creates distractions that reduce focus and efficiency, while also potentially increasing staff turnover.
Particularly concerning is how these issues compound over time. Small businesses often fall into a dangerous cycle: minor maintenance is deferred to save money, leading to major failures that drain financial resources, which further reduces the budget available for preventative maintenance. Breaking this cycle requires recognising that preventative safety measures represent investments rather than expenses.
Essential Preventative Checks Every Office Should Implement
Implementing a comprehensive safety check program doesn’t necessarily require significant financial investment. Many effective preventative measures can be conducted with minimal specialist equipment or expertise. The key lies in consistency and thoroughness rather than complexity.
Here are essential preventative checks that every office should incorporate into its regular maintenance schedule:
Monthly Visual Inspections:
- Examine all visible electrical cables, extensions, and power strips for damage, fraying, or overheating
- Check that all walkways remain clear of obstructions and trip hazards
- Verify that emergency exits remain unblocked and clearly marked
- Inspect lighting fixtures for proper operation and stability
- Check all smoke detectors and carbon monoxide alarms
Quarterly Technical Checks:
- Test emergency lighting systems to ensure proper operation during power failures
- Verify proper function of HVAC systems, including filter replacements
- Examine plumbing fixtures for leaks or slow drains that could cause water damage
- Test all GFCI outlets to ensure proper protection against electrical shocks
- Inspect all fire extinguishers for proper pressure and placement
Annual Professional Assessments:
- Simple procedures like routine PAT testing help identify unsafe appliances before they pose a risk to staff or property
- Professional inspection of electrical distribution panels and wiring
- A comprehensive review of fire safety systems, including alarms and suppression equipment
- HVAC system servicing and efficiency testing
- Structural assessment of any concerning areas (ceiling tiles, flooring, windows)
By distributing these checks throughout the year, businesses can manage the associated time and cost commitments more effectively. Many of the monthly and some quarterly checks can be assigned to appropriately trained staff members, while annual assessments typically require qualified professionals to ensure thorough evaluation and compliance with relevant standards.
Documentation plays a crucial role in this process. Each inspection should be recorded with dates, findings, and any corrective actions taken. These records serve multiple purposes: demonstrating regulatory compliance, supporting insurance claims if incidents do occur, and tracking patterns that might indicate developing problems requiring attention.
How These Checks Prevent Expensive Repairs

The financial benefits of preventative safety checks materialise through multiple pathways, each contributing to significant cost avoidance and operational stability. Understanding these connections helps businesses appreciate the return on investment these activities provide.
Early Detection of Electrical Issues: Electrical problems typically progress through detectable stages before causing catastrophic failures. Regular visual inspections can identify warning signs such as discoloured outlets, unusual odours, or warm equipment casings. Addressing these indicators promptly typically involves simple, inexpensive repairs rather than complete system replacements or fire damage restoration.
Extended Equipment Lifespan: Office equipment operates most efficiently and lasts longer when maintained properly. Regular cleaning, inspection, and minor adjustments help devices operate within their design parameters, reducing strain on components and extending useful life. This postpones major capital expenditures and improves the return on initial investments.
Prevention of Cascading Failures: In interconnected office environments, the failure of one system often affects others. For example, a malfunctioning HVAC system can lead to overheating that damages electronic equipment or a minor water leak can eventually cause structural damage and mould growth. Early intervention breaks these potential chain reactions before they begin.
Insurance Premium Stability: Insurers increasingly recognise and reward risk management efforts. Businesses that demonstrate consistent preventative maintenance through documented safety checks often qualify for premium discounts or more favourable terms. Moreover, having comprehensive records dramatically simplifies claims processes when incidents do occur, ensuring faster resolution.
Improving Your Office Safety Standards in 2025
As workplace models continue evolving in 2025, safety standards must adapt accordingly. The increasing prevalence of hybrid work arrangements, advanced technology integration, and changing regulatory expectations all influence how businesses should approach office safety.
Modern office safety extends beyond physical inspections to encompass a comprehensive safety culture. This includes:
Employee Awareness and Participation: Staff members represent the first line of defence in identifying potential safety issues. Providing basic training on recognising warning signs prevents employees from just staying silent and not reporting concerns before they escalate. Creating simple reporting mechanisms – whether digital forms or dedicated communication channels – ensures that observations translate into actions.
Digital Safety Management: Various software solutions now enable more systematic approaches to safety checks. These platforms typically offer customisable inspection templates, scheduling reminders, documentation storage, and trend analysis capabilities. For businesses managing multiple locations, these tools provide standardisation and centralised oversight.
Signage and Visual Communication: Strategic placement of safety information throughout office spaces reinforces awareness and provides immediate guidance during emergencies. Modern approaches incorporate QR codes linking to detailed procedures or interactive training materials, making information more accessible and engaging.
Integration with Facilities Management: Preventative maintenance isn’t just about avoiding problems – it’s about enhancing office safety standards in a way that creates a more productive, compliant, and confident workspace. This holistic approach treats safety as an integral component of facilities management rather than a separate consideration, ensuring more consistent implementation and oversight.
The evolution of safety standards also reflects changing priorities. While traditional concerns like fire safety and electrical hazards remain important, additional factors now receive greater attention:
- Indoor air quality monitoring and improvement
- Ergonomic assessments for both in-office and remote workers
- Mental health considerations within physical environments
- Accessibility accommodations for diverse workforce needs
- Sustainability integration with safety protocols
Organisations that recognise and adapt to these evolving standards position themselves advantageously – not just for compliance, but for operational excellence and employee satisfaction.
Building a Simple Safety and Maintenance Schedule
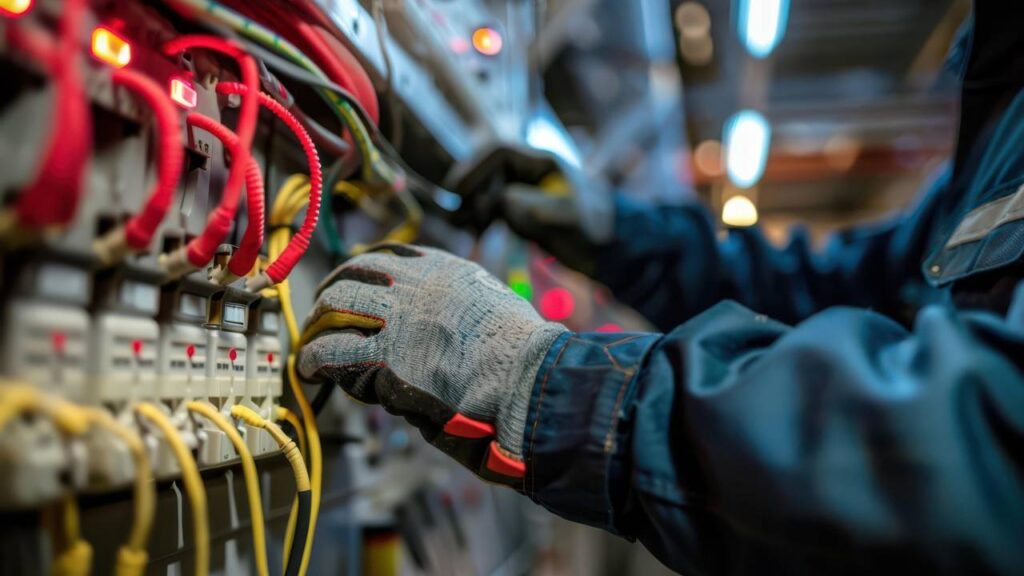
Creating an effective safety check system doesn’t require complex infrastructure. The following step-by-step approach provides a framework that even small businesses can implement with minimal resources:
1. Inventory Your Assets and Spaces Begin by documenting all equipment, systems, and areas requiring regular inspection. Categorise these based on criticality to operations, safety implications, and regulatory requirements. This inventory becomes the foundation for your inspection schedules.
2. Determine Appropriate Inspection Frequencies Assign inspection intervals based on manufacturer recommendations, industry best practices, regulatory requirements, and specific risk factors in your environment. High-use or high-risk items typically require more frequent checks than stable, low-risk systems.
3. Create Simple, Specific Checklists Develop clear inspection guidelines for each item or area, focusing on observable conditions that indicate potential problems. Effective checklists specify exactly what to look for rather than general instructions to “inspect” something.
4. Assign Responsibilities Determine who will conduct each type of inspection. While some checks require qualified professionals, many can be performed by staff members with appropriate training. Distributing responsibilities creates broader safety awareness while preventing inspection fatigue.
5. Implement a Documentation System Establish a consistent method for recording inspection results and tracking remediation efforts. This might range from simple spreadsheets to dedicated safety management software, depending on organizational size and complexity.
6. Set Up Reminder Systems Calendar notifications, task management software, or dedicated maintenance tracking applications can help ensure inspections occur as scheduled. These systems should include escalation procedures for checks that aren’t completed on time.
7. Review and Adapt Regularly Schedule quarterly reviews of your safety check system to identify any patterns in findings, assess effectiveness, and make necessary adjustments to frequency or focus areas.
Several digital tools can support this process without significant investment:
- Microsoft Teams or Google Workspace can host inspection checklists and documentation
- Trello or Asana provide visual task management for inspection scheduling
- Microsoft Forms or Google Forms can create simple inspection report templates
- Dedicated apps like iAuditor or Jolt offer more specialised features for safety inspections
The most effective systems balance comprehensiveness with practicality. Overly complex processes often lead to compliance fatigue and inconsistent implementation, undermining the entire preventative approach.
Conclusion
Preventative safety checks are one of the most cost-effective strategies for reducing office repair expenses and avoiding disruptive emergencies. By catching small issues early – whether it’s a frayed cable or a blocked HVAC drain – businesses can avoid unexpected costs, protect staff, and keep operations running smoothly.
For small Irish businesses, the shift from reactive fixes to proactive maintenance requires minimal investment but delivers long-term value. A structured safety check system not only improves compliance and workplace safety but also helps preserve budgets and enhances peace of mind.